Figura 1.27
Esquema de una columna empacada y elementos de empaque
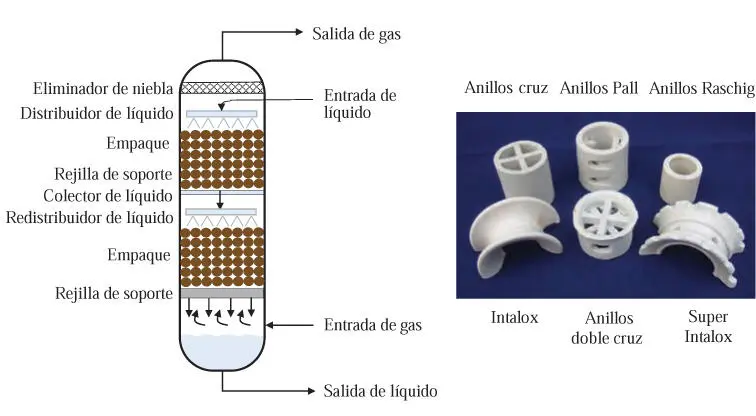
Elaboración propia a partir de Universitat Politecnica de Catalunya (s. f.)
5.4.2 Absorción con reacción en fase sólida
Este tipo de absorción emplea sustancias sólidas con alta superficie específica y se encuentra en el límite de la adsorción. La ventaja principal es que se generan productos finales que pueden deponerse fácilmente; por lo tanto, se producen menos emisiones de polvos y material particulado. Como ejemplo, se pueden apreciar las ecuaciones de las siguientes reacciones:
2HF (g)+ Ca(OH) 2(s)→ CaF 2(s)+ 2H 2O (l)2HCl (g)+ Ca(OH) 2(s)→ CaCl 2(s)+ 2H 2O (l)2SO 2(g)+ 2Ca(OH) 2(s)→ 2CaSO 3⋅ ½H 2O (s)+ H 2O (l)
El caso más característico de la aplicación de esta tecnología es la desulfuración de los humos de las plantas térmicas (en inglés, flue-gas desulfurization , FGD), emitidos por la combustión del azufre contenido en el combustible. Por ejemplo, el carbón tiene de 0,5 a 2 % de azufre, los petróleos residuales hasta 3 % y los residuos municipales hasta 50 %. En la atmósfera húmeda y por acción de la radiación UV, el SO 2se oxida a SO 3y se convierte en ácido sulfúrico, que genera la lluvia ácida.
El sistema de desulfuración de humos de una planta térmica se puede observar en la figura 1.28. En este, la caliza finamente molida es mezclada con agua para producir una suspensión que se pone en contacto con el gas sulfuroso por aspersión o salpicadura. El SO 2de los gases se convierte primero en CaSO 3. ½H 2O, pero luego, por acción del aire insuflado en la cámara, se convierte, finalmente, en CaSO 4. 2H 2O (yeso), que es inerte y puede ser separado fácilmente. Las reacciones son las siguientes:
• Combustión: S + O 2→ SO 2
• Absorción: CaCO 3+ SO 2→ CaSO 3+ CO 2
• Oxidación: CaSO 3+ ½O 2+ 2H 2O → CaSO 4• 2H 2O
Figura 1.28
Sistema de desulfuración de una planta térmica
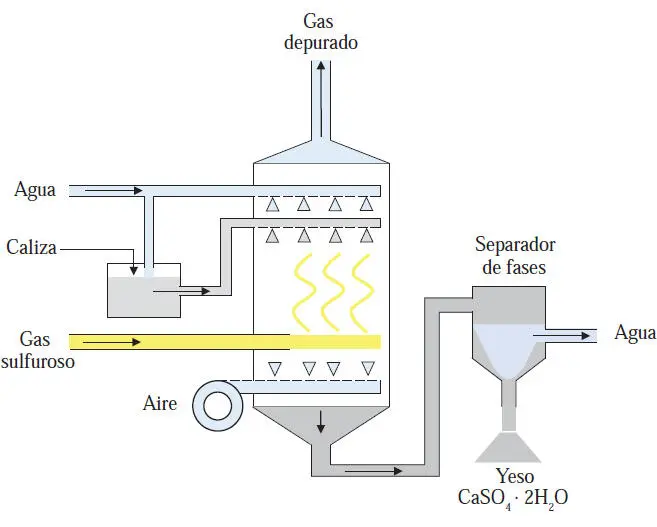
Elaboración propia a partir de Langermann (2014)
La adsorción es otra técnica de separación basada en el equilibrio y que utiliza un material adicional: un sólido poroso de alta superficie específica que tiene afinidad con gases y líquidos (Murphy, 2007). El equipo es similar a una columna de absorción empacada, pero de menor altura. En este caso, la diferencia es que el empaque es un sólido activo, capaz de retener sustancias gaseosas y solutos. Asimismo, el proceso es discontinuo, es decir, una vez saturado el sólido, se debe iniciar una etapa de regeneración para separar la sustancia adsorbida y preparar el sólido poroso para un nuevo ciclo de adsorción. La figura 1.29muestra el esquema de una columna de adsorción.
Figura 1.29
Esquema de una columna de adsorción
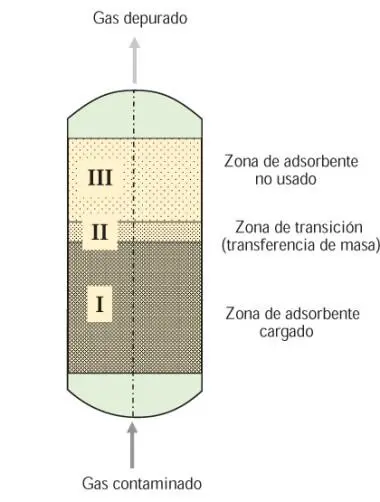
Elaboración propia a partir de Langermann (2014)
Las típicas sustancias adsorbentes son el carbón activado, las zeolitas y el gel de sílice. Entre las aplicaciones comunes de la adsorción se encuentran la recuperación de solventes, la eliminación de olores y sustancias tóxicas, la desulfuración de gases y la limpieza de gas natural. Los adsorbentes deben reunir ciertas características como alta capacidad y velocidad de adsorción, así como tienen que regenerarse fácilmente y ser hidrofóbicos (resistencia al vapor de agua). Existen los siguientes métodos de regeneración:
• Ciclo de variación térmico
El adsorbente es calentado con un gas caliente de purga para remover el adsorbato. Finalmente, el lecho debe ser enfriado, de modo que pueda ser usado en el siguiente ciclo de adsorción. El tiempo de regeneración es de pocas horas.
• Ciclo de variación de presión
En este caso, el lecho se desorbe al reducir la presión a temperatura constante. El tiempo de regeneración es corto comparado con el ciclo térmico.
• Ciclo de purga con gas inerte
El adsorbato se remueve con un gas no adsorbente o inerte a través del lecho. El tiempo de regeneración es de pocos minutos.
• Ciclo de purga de desplazamiento
Se mantiene la presión y la temperatura constantes, pero se usa un gas o líquido que se adsorbe más que el adsorbato. Al igual que en el caso anterior, el tiempo de regeneración es de pocos minutos.
5.4.4 Depuración catalítica
La depuración catalítica busca transformar el contaminante mediante reacciones de oxidación, reducción o descomposición en sustancias inertes o menos tóxicas. Por ejemplo, la eliminación de óxidos de nitrógeno de gases de combustión con catalizadores sólidos como TiO 2, V 2O 5, Fe 2O 3e inyección de NH 3:
4NO + 4NH 3+ O 2→ 4N 2+ 6H 2O 2NO 2+ 4NH 3+ O 2→ 3N 2+ 6H 2O
El proceso se conoce como reducción catalítica selectiva (SCR, por sus siglas en inglés). Ha sido implementado ampliamente en plantas térmicas y también en la industria del cemento, cuando se usan combustibles alternativos (llantas usadas, residuos sólidos). Como se observa en la figura 1.30, los gases de combustión provenientes del caldero (generador de vapor) se mezclan con aire fresco y vapor de amoniaco, luego se inyectan a la cámara del reactor SCR. Dentro del reactor hay bloques de catalizador poroso, y los óxidos de nitrógeno y el amoniaco se convierten en productos inertes (nitrógeno y vapor de agua). En otra variante de este proceso, llamada reducción catalítica no selectiva (NSCR, por sus siglas en inglés), se inyecta también un combustible (gas natural, GLP) y los productos también contienen CO 2.
Figura 1.30
Sistema de reducción catalítica selectiva para depuración de NOx y catalizador monolítico
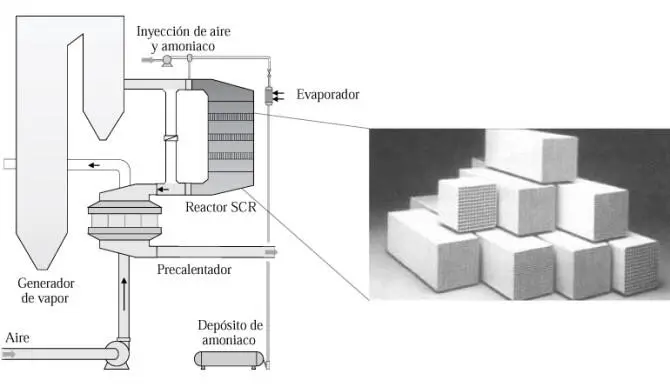
Elaboración propia a partir de Langermann (2014)
Un proceso combinado, conocido como DeSONO x, permite la eliminación de gases sulfurosos y óxidos de nitrógeno. Se lleva a cabo en las siguientes etapas:
• Filtro electrostático seco
• Inyección de NH 3y eliminación de óxidos de nitrógeno (DeNO x)
• Eliminación de óxidos de azufre (DeSO x)
• Lavado en varias etapas
• Filtro electrostático húmedo
La depuración térmica tiene como objetivo la rápida poscombustión y oxidación total de sustancias contaminantes como hidrocarburos clorados, gases con alta carga orgánica, fosgeno, vapores de cianuro de hidrógeno, compuestos sulfurados, nitrosos, amidas, etcétera, que se encuentran en plantas térmicas, especialmente en aquellas que utilizan residuos municipales como combustible. La formación de compuestos altamente contaminantes, como las dibenzodioxinas policloradas (PCDD) y los dibenzofuranos policlorados (PCDF), provienen de la fracción orgánica y de polímeros presentes en los residuos sólidos urbanos. En el proceso denominado De-DIO x, se emplean catalizadores mixtos de TiO 2, WO 3, V 2O 5, que son muy selectivos para la degradación de los contaminantes y logran una concentración muy baja de los mismos en los gases residuales (según las normas legales). Los catalizadores son, además, muy estables y, a temperaturas adecuadas (> 190 °C), se evita la desactivación por adsorción de los contaminantes en la superficie.
Читать дальше