Figura 1.21
Esquema de funcionamiento de un filtro de mangas
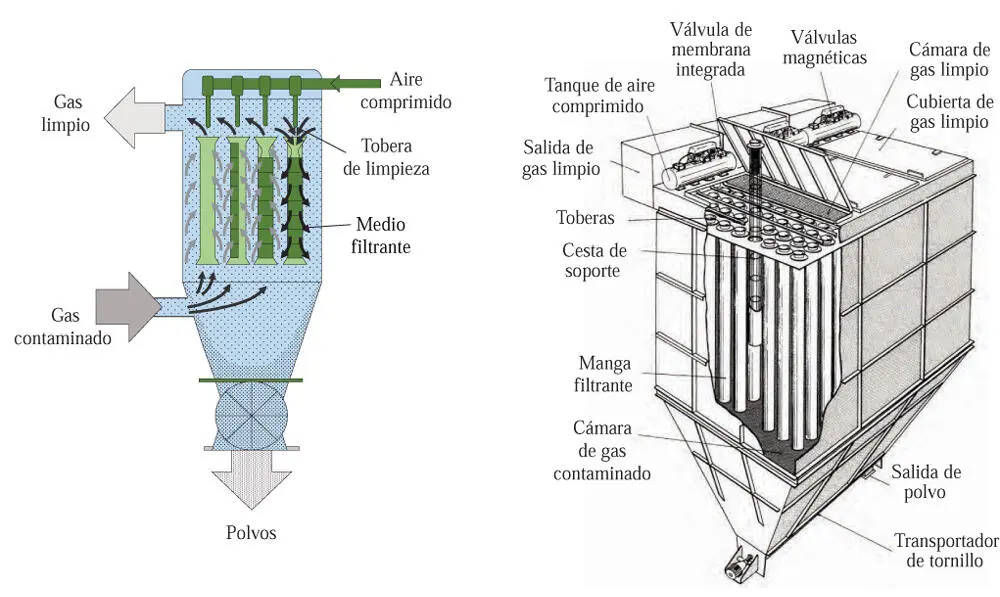
Elaboración propia a partir de Langermann (2014)
Las torres o cámaras de lavado (en inglés, scrubbers ) tienen como objetivo la unión de las partículas sólidas mediante una fase líquida, principalmente agua, por principios de difusión, carga eléctrica, condensación e inercia de masa (véase la figura 1.22). Existen diversas formas de captura de las partículas; puede ser a través de una capa de líquido, a través de un empaque, a través del flujo a lo largo de una superficie o por la distribución de gotas líquidas en la fase gaseosa.
Figura 1.22
Métodos diversos para el lavado de gases
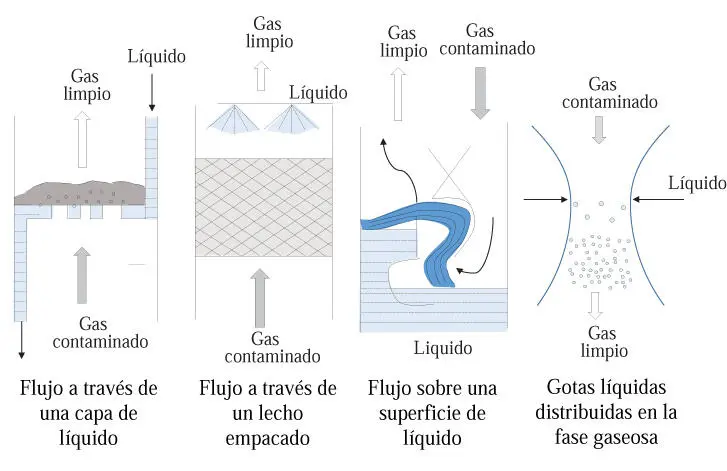
Elaboración propia a partir de Langermann (2014)
En otra variante de las cámaras de lavado de gases, se utilizan toberas de Venturi para producir una presión negativa que aspira el líquido y logra así el contacto con las partículas de polvo. Estos equipos suelen ser más compactos y eficientes que las torres o cámaras convencionales de lavado, pero tienen un mayor consumo de energía y más desgaste, debido a la alta velocidad de flujo en las toberas, además de que generan ruido. En la figura 1.23, se puede observar el esquema de funcionamiento de un lavador de Venturi.
Figura 1.23
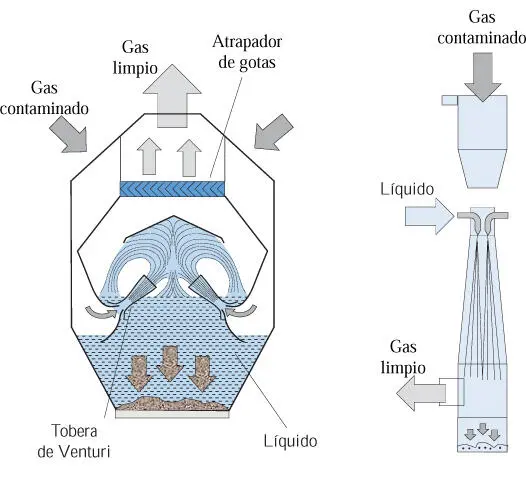
Elaboración propia a partir de Langermann (2014)
5.2.4 Precipitadores electrostáticos
Los precipitadores electrostáticos, también llamados filtros electrostáticos o electrofiltros, utilizan una alta diferencia de potencial (hasta 50 kV) para cargar eléctricamente la superficie de las partículas y trasladarlas de este modo a la superficie con la carga opuesta. Internamente, en el cátodo (negativo), se genera el denominado efecto corona por la alta tensión, que ioniza las moléculas neutras del gas, las cuales a su vez cubren la superficie de las partículas. La atracción electrostática entre las partículas cargadas negativamente y la superficie del ánodo (positivo) hace que las partículas se desplacen y se separen. En algunos casos, se inyecta también una niebla de agua para mejorar la separación. El uso de estos electrofiltros es muy común en las centrales térmicas de carbón y en la industria metalúrgica. En la figura 1.24, se observa el principio de operación, así como un ejemplo de aplicación.
Figura 1.24
Principio de aplicación de un precipitador electrostático
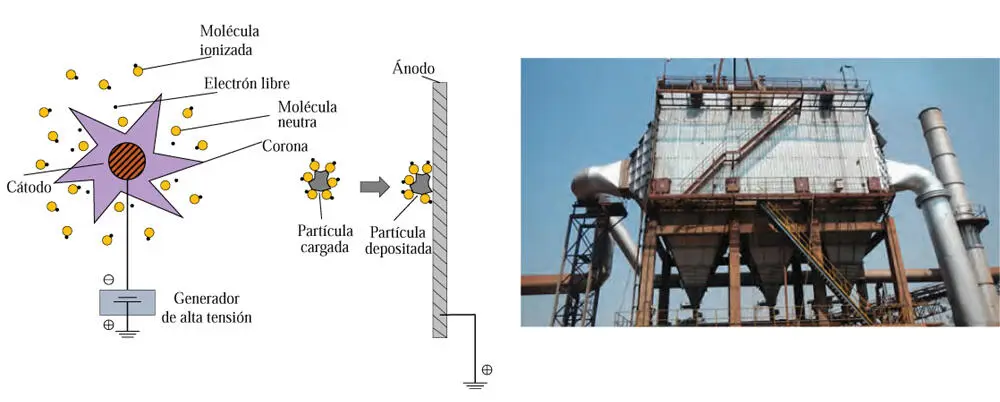
Elaboración propia a partir de Langermann (2014)
La tabla 1.7presenta un cuadro comparativo de las características de los equipos de separación de polvos: ciclón, electrofiltro y torre de lavado.
Tabla 1.7
Comparación de los equipos de separación de polvos
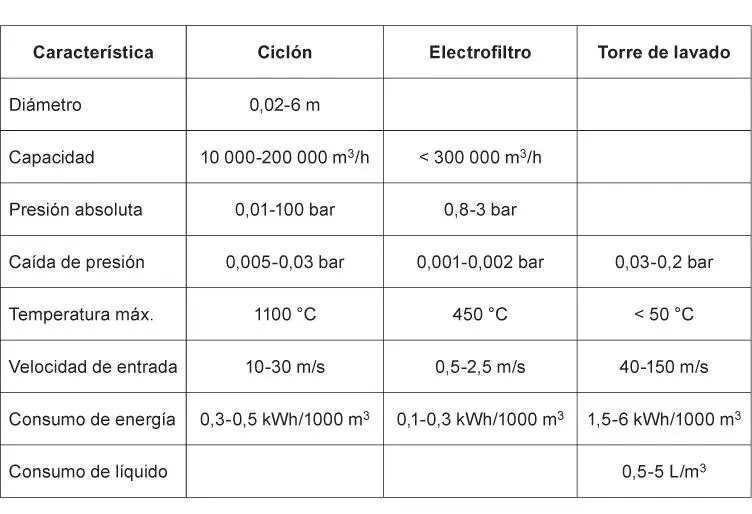
Fuente: Langermann (2014)
5.3 Separación de líquidos
Técnicamente, en este tipo de operaciones, las gotas de líquido en una corriente gaseosa se comportan en forma similar a las partículas, y es frecuente la separación simultánea de partículas y gotas (aerosoles). Los equipos más usuales son los separadores de impacto y los condensadores; si se emplea un gas criogénico como nitrógeno líquido, se denominan criocondensadores (véase la figura 1.25).
Figura 1.25
Esquema de separación de líquidos por impacto y condensación
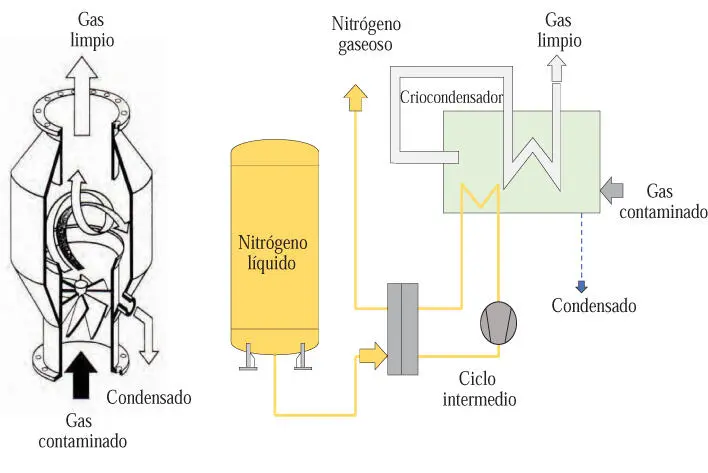
Elaboración propia a partir de Langermann (2014)
5.4 Separación de gases
5.4.1 Absorción
La absorción es una técnica de separación que se basa en el equilibrio, mediante la cual una corriente gaseosa es puesta en contacto con un líquido (el absorbente) que disuelve selectivamente uno o más componentes de la corriente gaseosa (Murphy, 2007). El principio es la solubilidad del gas en el absorbente, pero también se puede dar la absorción química, donde el gas reacciona con el líquido absorbente. Esta técnica se denomina también lavado (inglés, scrubbing ) cuando se emplea para depurar emisiones gaseosas.
El equipo característico para la absorción es la columna empacada, que cuenta con uno o más lechos de elementos inertes (el relleno o empaque), aunque se usa, asimismo, la columna de platos. Su objetivo es mejorar el contacto entre el gas y el líquido. El gas ingresa por la parte inferior y asciende a través del lecho empacado mientras se pone en contacto con el absorbente, que se alimenta por la parte superior mediante un distribuidor. El absorbente cargado (solución rica) se colecta en la parte inferior y se envía a otra columna (columna de separación o desorción, del inglés stripping ) para recuperar el componente absorbido como gas concentrado, y el absorbente despojado (solución pobre) es usado una vez más en la etapa de absorción.
La absorción es favorecida por bajas temperaturas y presiones elevadas; ocurre lo contrario en la desorción, que requiere altas temperaturas y bajas presiones. De manera ideal, el solvente debe ser muy selectivo, poco volátil y estable térmicamente. En la práctica, sin embargo, estas condiciones no se dan, por lo que debe reponerse el solvente que se pierde con la corriente gaseosa y que se descompone; además, el gas concentrado puede contener otros componentes no deseados. En la figura 1.26, se aprecia un típico sistema de depuración de gases contaminados por lavado.
Figura 1.26
Sistema de depuración de gases por lavado (absorción-desorción)
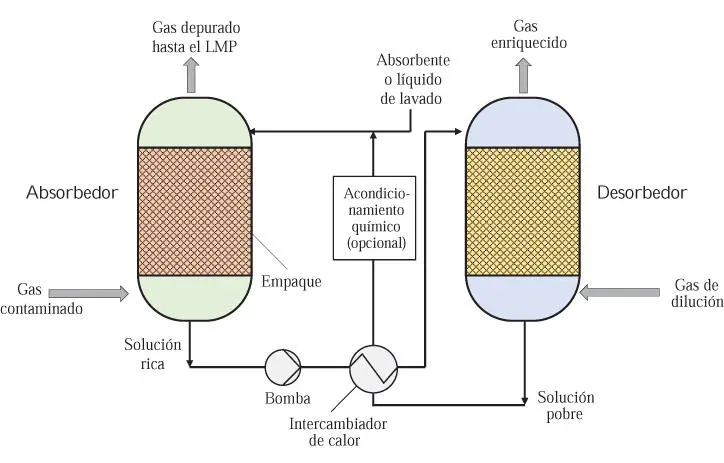
Elaboración propia
La tabla 1.8presenta una lista parcial de absorbentes y soluciones de lavado típicas usadas en la industria. A continuación, la figura 1.27detalla el sistema de una columna empacada y algunos tipos de elementos de empaque.
Tabla 1.8
Lista de algunos absorbentes comunes
Sustancia que se va a separar |
Absorbentes |
HCl |
Agua, álcalis, carbonatos |
NH 3 |
Agua, ácidos |
Alcoholes, acetona |
Agua, aceites |
H 2S, R-SH |
Solventes orgánicos (alcanol, aminas) |
CO 2 |
K 2CO 3, metanol, solventes orgánicos |
COS, HCN |
Solventes orgánicos |
SO 2(desulfuración) |
Lechada de cal, caliza, soda, solución de NH 3 |
NO x |
Solución de NH 3 |
H 2O (secado de gases) |
TEG (trietilén glicol), H 2SO 4concentrado |
Elaboración propia
Читать дальше