Praxair's developments present a tubular geometry where OTM tubes and CH 4reforming tubes are combined in systems for oxy‐combustion and syngas production applications by using advanced boilers and heaters in combustion processes [59–61]. As it can be observed in Figure 3.5d, Praxair's OTM concept consists of a multi‐panel tubular reactor system where natural gas steam reforming, O 2separation, and autothermal reforming is carried out by using integrated U‐shaped reformer and OTM tubes.
Research centers such as RWTH‐Aachen and the Fraunhofer Institute for Ceramics Technologies and Systems (IKTS) – both located in Germany – are conducting other of the most advanced developments in the OTM field. RWTH‐Aachen designed, fabricated, and tested in a realistic environment an OTM module within the OXYCOAL‐AC Project [62, 63]. The main aim of this development was to demonstrate a zero‐CO 2emission proof of concept for coal‐fired power plants using an OTM module as an O 2supply unit for conducting and oxy‐combustion [64]. For that, an OTM module was developed consisting of BSCF tubular membranes (15 m 2membrane area with 570 tubes) with a production capability of 0.6 TPD O 2, generating up to 120 kW by combusting pulverized coal. With regard to IKTS, which are specialized in the manufacturing and testing of 3‐end OTM module systems considering BSCF tubes, they constructed the first stand‐alone O 2production unit in 2009 producing 2.7 l min −1O 2at 850 °C [65], being later improved achieving up to 2 kg O 2h −1(23.3 l min −1).
As previously mentioned, the impact of the CO 2emissions on Earth is triggering the energetic transition from fossil fuels to environmentally friendly energy sources. H 2is a promising energy carrier allowing the storage of chemical energy; nowadays, its main use is as a reactant for the synthesis of NH 3and CH 3OH, in the refining and other industrial applications. H 2can be used in fuel cell cars, as feed into the natural gas network, and in H 2/O 2fuel cells among others [66–69].
Therefore, H 2separation is an important process and its utility has been demonstrated over the past years. Pressure gradient is the main driving force for H 2separation in these type of membranes, giving a large H 2partial pressure, hydrogen will migrate across the membrane. These membranes operate at a wide range of temperatures, and they can be divided into six different types depending on their properties, temperature ranges, and H 2permeation performance. Table 3.1shows a comparison between H 2‐selective membranes.
Among these membranes, mixed protonic–electronic conductor (MPEC)‐based membranes are the most appropriate candidates for application to high‐temperature H 2(>500 °C) separation‐based processes. These membranes allow to separate H 2because of their ambipolar conductivity (electronic and protonic) when a hydrogen partial pressure difference is applied across the membrane [72–76]. This technology is the focus of many research groups worldwide because it offers the advantage of process intensification by shifting the thermodynamic equilibrium of a reaction [77–79].
3.4.1 Proton Defects in Oxide Ceramics
In an environment containing hydrogen or water, protons are dissolved in the oxide lattice forming positively charged defects following Eq. (3.6)written in Kröger–Vink notation [78].
is a positively charge (2+) oxygen vacancy,
represents an oxygen atom with a neutral charge placed on its original place in the crystal lattice, and
is a proton defect (+1 charged).
Table 3.1Hydrogen‐selective membrane types [70, 71].
Source: Adapted from Kluiters [70] and Al‐Mufachi et al. [71].
|
Dense polymer |
Microporous ceramic |
Dense metallic |
Porous carbon |
Dense ceramic |
Temperature range (°C) |
<100 |
200–600 |
300–600 |
500–900 |
600–900 |
H 2selectivity |
Low |
5–139 |
>1000 |
4–20 |
>1000 |
H 2flux (×10 −3mol m −2s −1) DP = 100 kPa |
Low |
60–300 |
60–300 |
10–200 |
6–80 |
Stability issues |
Swelling, compaction, mechanical strength |
Stability in H 2O |
Phase transition |
Brittle, oxidizing |
Stability in CO 2 |
Poisoning issues |
HCl, SO 2, CO 2 |
|
H 2S, HCl, CO |
Strong adsorbing vapors, organics |
H 2S |
Materials |
Polymers |
Silica, alumina, zirconia, titania, zeolites |
Pd alloy |
Carbon |
Proton conducting ceramics (mainly SrCeO 3, BaCeO 3) |
Transport mechanism |
Solution/diffusion |
Molecular sieving |
Solution/diffusion |
Surface diffusion; molecular sieving |
Solution/diffusion (proton conduction) |
Development status |
Commercial by air products, Linde, BOC, and Air Liquide |
Prototype tubular silica membranes available up to 90 cm. Other materials only small samples (cm 2) |
Commercial by Johnson Matthey; prototype membrane tubes available up to 60 cm |
Small membrane modules commercial, mostly small samples (cm 2) available for testing |
Small samples available for testing |
(3.6) 
The equilibrium constant of proton defect formation reaction in oxide ceramic materials ( K OH·) is depicted in Eq. (3.7), where
represents the proton defect concentration,
is the oxygen vacancy concentration,
represents the concentration of oxygen atoms with a neutral charge placed on its original place in the crystal lattice, and p H2Ois the water vapor pressure.
(3.7) 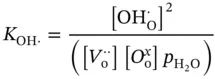
For large bandgap oxide materials (e.g. Ce, Ti, and Zr), the formation of proton defects at moderate temperatures takes places through the dissociative absorption of water [80]. Water dissociates into a hydroxide ion and a proton, the hydrogen ion then occupies an oxide ion vacancy, and the proton forms a covalent bond with a lattice oxygen. The formation of proton defects implies a significant weight gain; hence, the concentration of such defects can be measured by thermogravimetric analysis (TGA) as a function of temperature and water partial pressure.
3.4.2 Proton Transport Membrane Fundamentals
Understanding the mechanism of proton conduction is of utmost importance for the development of novel materials. It is generally accepted that proton diffusion in protonic conductors occur via the Grotthuss‐type mechanism assisted by water molecules [81–83]. Moreover, hydrogen separation is driven by the hydrogen partial pressure difference across the membrane.
Читать дальше