4 The substrate must demonstrate good physicochemical stability during storage.
5 The medium must be easy to sterilize by usual techniques since certain media could be viscous or very heavily loaded with solid matter that affect the sterilization efficiency.
6 The medium must have an acceptable viscosity, since a too viscous medium is unfavorable for the aeration and homogenization of the substrate, in addition to causing a higher energy demand for agitation and a greater risk of formation of unwanted foam.
7 The raw materials must be able to guarantee the quality of the finished product (i.e. be free of toxic substances) and have the lowest possible content of impurities to facilitate the recovery and purification stages at the end of the process.
Any industrial fermentation aims to produce a molecule of interest in the highest quantity, in the shortest time, and at the lowest possible cost. For this, a microorganism must be cultivated under controlled physicochemical conditions within a large volume enclosure specially designed for this purpose: the bioreactor or fermenter. One of the most used bioreactors at the industrial scale is the stirred tank type, schematized in Figure 1.9. Other types of bioreactors exist and are described in Chapter 2.
Mainly, two types of bioreactors exist. The first one allows performing nonaseptic cultures such as brewing and effluent treatment, and the second one requires aseptic conditions for successful product formation, such as antibiotics, vitamins, polysaccharides, and recombinant proteins. Aseptic bioreactors can be sterilized repeatedly and can process a large volume of culture. Several peripheral systems are coupled to the tank and allow controlling automatically the parameters affecting the microbial growth such as the temperature, the pH, and the dissolved O 2. Within the bioreactor, the microorganisms are suspended in the aqueous nutrient medium containing the necessary substrates for microbial growth and product synthesis. Changing the culture conditions has a great impact on the bioprocess performances, as discussed in Chapter 3.
Figure 1.9 Fermenter vessel schematic and terminology.
Source: Charles (1999).
In a bioreactor, fermentation occurs in a multiphase state: a gas phase where CO 2, O 2, and N 2can be exchanged, a liquid phase mainly composed of the aqueous medium, and a solid phase mainly composed of microorganisms and solid substrates. These phases must be perfectly mixed to ensure the most efficient and homogenous heat and mass transfer. To ensure a perfect mixing of the suspension, the shaft of the bioreactor is usually equipped with several impellers. Although a wide range of impeller types exist in the market, the six flat‐bladed (Rushton) turbine impellers are used in the majority of bioreactors. Usually, three to five impellers are mounted and spaced at intervals equivalent to one tank diameter along the shaft to avoid a swirling type of liquid movement.
An optimal production system could be achieved by taking a few requirements that include:
1 Avoiding the contamination of the culture, which can be achieved by designing a bioreactor where the inputs and outputs of the fermenter are controlled;
2 No leakage or water evaporation from the medium can occur;
3 Agitation of the medium should be perfect to allow a homogenous distribution of O2 in the medium and the maintenance of O2 concentration above the critical value; and
4 The fermentation parameters that include the pH, temperature, etc. must be automatically controlled.
A successful process occurs when all the parameters required for the growth and production of a molecule of interest are brought together. Yield and productivity constitute the two main aspects to be quantified during fermentation. They indicate the conversion efficiency of the substrate into cells and products. The following equations are given for culture in batch mode.
The yield in biomass Y X/Sis given by Eq. (1.3)and corresponds to the mass (g) of dry cell biomass produced per gram of substrate consumed (g g −1).
(1.3) 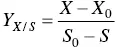
where X 0and X correspond, respectively, to the initial and final biomass concentrations (g l −1). S 0and S correspond, respectively, to the initial and final carbon substrate concentrations (g l −1).
The yield in product Y P/Sis given by Eq. (1.4)and corresponds to the weight in grams of product produced per gram of substrate consumed (g g −1).
(1.4) 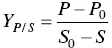
where P 0and P correspond, respectively, to the initial and final product concentrations (g l −1). S 0and S correspond, respectively, to the initial and final carbon substrate concentrations (g l −1).
The productivity in biomass P Xis given by Eq. (1.5)and corresponds to the weight in grams of biomass produced per liter of culture per hour (g l −1h −1).
(1.5) 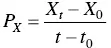
where X 0and X tcorrespond, respectively, to the initial biomass concentration and that at time t (g l −1). t 0and t correspond, respectively, to the initial and final time (h).
The productivity in product P pis given by Eq. (1.6)and corresponds to the weight in grams of product produced per liter of culture per hour (g l −1h −1).
(1.6) 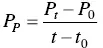
where P 0and P tcorrespond, respectively, to the initial product concentration and that at time t (g l −1). t 0and t correspond, respectively, to the initial and final time (h).
This chapter summarized the different steps to conduct a conventional fermentation with a special emphasis on energy metabolism, the different microorganisms used at industrial scale, as well as process parameters and performances. Nonetheless, the field of bioprocesses includes as well the culture of plant and animal cells, algae, and environmental processes. After fermentation, depending on the intracellular or extracellular localization of the synthesized product, cell lysis is required before starting the different downstream processing steps. Fermentation optimization could be performed using different approaches such as the use of the design of experiment approach and the implementation of emerging technologies to assist the fermentation.
1 Actis, L.A., Tolmasky, M.E., and Crosa, J.H. (1999). Bacterial plasmids: replication of extrachromosomal genetic elements encoding resistance to antimicrobial compounds. Front. Biosci. (4): D43–D62.
2 Angelidaki, I., Karakashev, D., Batstone, D.J. et al. (2011). Biomethanation and its potential. In: Methods in Enzymology, Methods in Methane Metabolism, Part A (eds. A.C. Rosenzweig and S.W. Ragsdale), 327–351. Academic Press.
3 Bérdy, J. (2005). Bioactive microbial metabolites. J. Antibiot. (Tokyo) 58: 1–26.
4 Campbell, M.K. (2015). Biochemistry. Belmont, CA: Cengage Learning Brooks/Cole. ed.
Читать дальше