The first circulating conduit 43 may include a first control valve 46 installed to control steam to be supplied to the first fluid flows 41. The second fluid flows 51 are spaced a predetermined distance apart from the bottom surface of the lower mold 30 toward the cavity 12. The second fluid flows 51 are connected to each other by communication holes 52. In addition, the second fluid flows 51 are sealed by a blocking plate 53 engaged with the lower mold 30. The blocking plate 53 may have partitioning plates 54 inserted into the second fluid flows 51 to elongate a fluid flow track of the second fluid flows 51. Here, each of the partitioning plates 54 may be shorter than each of the second fluid flows 51.
Figure 1.1 Weldless-type injection mold apparatus (24).
The first cooling unit 50 includes a first refrigerant supply unit 55 for continuously supplying coolant to the second fluid flows 51. The first refrigerant supply unit 55 includes a first refrigerant tank 57 in which refrigerant 56 such as coolant or cooling oil is stored, a first pump 58 connecting the refrigerant tank 57 and the first fluid flow 51, and a third circulating conduit 59. The first refrigerant tank 57 is connected to a makeup water tank 57a for refilling the refrigerant 56. In addition, a refrigerant cooling system for cooling the refrigerant may be installed in the first refrigerant tank 57.
The third fluid flows 61 and the branch conduit 71 may be connected to each other by the first circulating conduit 43 of the boiler 42 and a purge conduit 73, so that the refrigerant of third fluid flows 61 may be exhausted when heating is carried out by the heating unit 40. The second control valve 72 may be a three-way valve installed at a connection part of the purge conduit 73 and the branch conduit 71 to supply steam or coolant.
Images of the upper mold and the lower mold during injection molding were obtained using a forward-looking infrared camera. This can illustrate the heated states during injection molding, as shown in Figure 1.2.
As evident from the photographs in Figure 1.2, heat accumulated around the cavity, while heat did not accumulate in the upper and lower molds. That is to say, since heat is not transferred to a lower portion of the cavity, the heat capacity for the overall injection molding process is not so high.
Since heat accumulation is prevented in such a manner, a cooling and heating time for injection molding, specifically the cooling time, can be reduced, thereby shortening the overall cycle time required for injection molding of a product, ultimately enhancing the manufacturing efficiency (24).
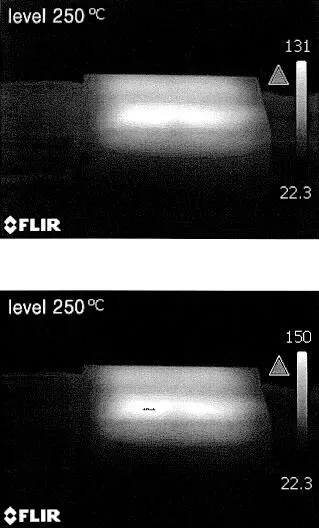
Figure 1.2 Heated states during injection molding (24).
1.6.2.2 Lamellae Orientation of Isotactic Poly(propylene)
Earlier reported studies on RHCM focused mainly on controlling the mold temperature distribution and temperature history (22, 25) as well as the relationship between process parameters and macroscopic properties of parts (9, 22).
Although it is well known that the morphology determines the macroscopic properties of parts, there are only a few studies on morphologies in the RHCM part.
Isotactic poly(propylene) (iPP) is a typical crystalline polymer with polymorphism that is commonly used to study the relationship between the molding process, morphology, and part quality in injection molding (26). A multilayered structure was prepared that was divided into the skin layer, shear layer, and core layer depending on the morphology. In particular, the crystal was highly oriented in the skin layer, there were a large number of fibrous shish-kebab crystal structures in the shear layer, and there were spherulite crystal structures in the core layer.
The thickness difference of the multilayered structures, crystallization and lamellae orientation at different sampling sites or molding and between RHCM and conventional injection molding (CIM) processes also reflected the variations of the temperature and shear gradient during the filling process.
The main difference between these two processes was the different temperature histories in the mold, which introduced various thermal and shear histories to the polymer. Accordingly, the multilayered structures differed from each other, which could be observed from SEM images (26).
In the CIM part, the degree of lamellae orientation was also roughly centro-symmetric, which increased and then decreased from the skin layer to the core layer. The degree of lamellae orientation reached a maximum at the shear layer and a minimum at the core layer. For the RHCM part, the degree of lamellae orientation of the different layers varied slightly, and the degree of lamellae orientation of all layers was less than those in the CIM part. The maximum degree of lamellae orientation was at the skin layer next to the moving half, and it decreased slightly to a minimum at the core layer. Then it increased slowly until reaching the skin layer next to the heated stationary half, at which point the degree of lamellae orientation was less than that of the opposite skin layer. The variation of lamellae orientation was attributed to the different flow and temperature histories of the RHCM and CIM molding processes (26).
1.6.3 Injection Molding: Heating
1.6.3.1 Modeling a Fast Mold Temperature
The modulation of the mold temperature during injection molding is a strategic issue since it allows modulating and calibrating interesting properties of the moldings (27).
Thin heating devices (28) were layered on the cavity surface allowing its fast temperature evolution between injection and cooling channels temperatures.
The heating device was made up of four layers (27): an 80 µm thick electrically conductive layer of carbon black loaded poly(amide imide), which induces the cavity surface heating by Joule effect, two Kapton electrically insulating layers, one on each side of the electrically conductive layer. A steel layer, 100 µm thick, protects the heating device from the incoming melt. The heating power was chosen such that, when the polymer reaches the cavity, the cavity surface temperature was intermediate between the mold temperature, as held by the cooling channel, and the injection temperature.
The heating devices were made by a conductive layer between two insulating layers with thicknesses selected in order to realize a heating/cooling cycle as fast as possible.
Several tests were performed, injecting iPP, using different heating powers and heating times to analyze the effect of the fast cavity surface temperature evolution on the molding morphology and properties. The heat transfer through the mold was modeled, accounting for the Joule effect in the conductive layer of the heating devices (27).
The injection molding process coupled with the system designed to achieve a fast evolution of the cavity surface temperature can be considered a multiphase process (because during the process the polymer in the cavity changes from the molten to the solid state) during which there is a transient heat transfer in the mold (including the multilayer heating device) that has to be considered simultaneously and combined with the transient heat transfer in the flowing polymer. Commercial software can be adopted to analyze this combination of transient processes but the solution can be obtained only adopting a serial combination of the analysis of the two different processes (27):
Читать дальше