C. Anandharamakrishnan - 3D Printing of Foods
Здесь есть возможность читать онлайн «C. Anandharamakrishnan - 3D Printing of Foods» — ознакомительный отрывок электронной книги совершенно бесплатно, а после прочтения отрывка купить полную версию. В некоторых случаях можно слушать аудио, скачать через торрент в формате fb2 и присутствует краткое содержание. Жанр: unrecognised, на английском языке. Описание произведения, (предисловие) а так же отзывы посетителей доступны на портале библиотеки ЛибКат.
- Название:3D Printing of Foods
- Автор:
- Жанр:
- Год:неизвестен
- ISBN:нет данных
- Рейтинг книги:3 / 5. Голосов: 1
-
Избранное:Добавить в избранное
- Отзывы:
-
Ваша оценка:
- 60
- 1
- 2
- 3
- 4
- 5
3D Printing of Foods: краткое содержание, описание и аннотация
Предлагаем к чтению аннотацию, описание, краткое содержание или предисловие (зависит от того, что написал сам автор книги «3D Printing of Foods»). Если вы не нашли необходимую информацию о книге — напишите в комментариях, мы постараемся отыскать её.
Explore the fascinating realm of 3D food printing and its applications 3D Printing of Foods
3D Printing of Foods
3D Printing of Foods
3D Printing of Foods — читать онлайн ознакомительный отрывок
Ниже представлен текст книги, разбитый по страницам. Система сохранения места последней прочитанной страницы, позволяет с удобством читать онлайн бесплатно книгу «3D Printing of Foods», без необходимости каждый раз заново искать на чём Вы остановились. Поставьте закладку, и сможете в любой момент перейти на страницу, на которой закончили чтение.
Интервал:
Закладка:
Scanning mode | Scan range | Scanning principle | Description | Commercial scanners |
---|---|---|---|---|
Non‐contact | Short range | Laser triangulation‐based 3D technology | Projects a laser light source onto the surface of the object and determine the amount of deformed light reflected from the surface | Sense 3D scanner |
Structured light‐based 3D technology | Uses trigonometric triangulation of the structured light (white/blue). It measures the deformed light pattern from the surface of object based on digital light processing (DLP) technique | EinScan, EinScan Pro 2X | ||
Long range | Pulse‐based laser | Based on laser beam’s time of flight. The projected laser light is collected by sensor and time of travel between emission and reception provides surface details | Lidar 3D scanner | |
Phase shift laser | In addition to pulse‐based scanner, these systems modulate power of the laser thereby it allows comparison of the phase of the laser emitted and returned to the sensor | Lidar 3D scanner | ||
Contact | Medium range | Coordinate measuring machine (CMM) | Involves measuring the degree of deformation of a probe by scanning several coordinate points on object’s surface | Altera SL bridge CMM |
Arm‐based 3D scanners | Similar to CMM with additional provisions attachable 3D scanner unit for collecting large amount of points | Hexagon’s ROMER Absolute Arm scanner | ||
Optically tracked 3D scanners | It uses a set of cameras to capture and track the location of scan in working space | Hexagon’s Leica Absolute Scanner and Creaform’s Metrascan 3D scanner |
1.8.2 Repairing and Post‐Processing
After the acquisition of the image, the captured 3D models are processed adequately to restore better precision and higher resolution during 3D printing. Scanned 3D models are subjected to digital processing to improve the quality of the acquired image. Any 3D solid files would be stored in STL form which is described in terms of small clustered triangular facets forming the 3D object (Szilvśi‐Nagy and Matyasi 2003; Wu and Cheung 2006). This format follows four basic principles such as common vertex, orientation rule, closed facets, and must have non‐negative coordinate values. Some of the common STL errors ( Figure 1.8) and their causes are as follows: holes – caused by missing of facets during triangulation; gaps – occurs due to dislocation of vertices forming a boundary between the pairs; dislocation – a common error that occurs during computation when the same vertex is shared by two triangular facets; reverse oriented normal – a disordered pattern occurs when triangular facets fail to follow orientation rule; overlaps – inaccuracy during computation causes merging of facets one above the other; and redundancy – independent triangular facets stick out the regular topological structure (Liu et al. 2009). Common vertex is the sharing of two edges by the adjacent triangular facets. The orientation rule implies that the normal vector of the individual facets must follow the right‐hand rule and it should point towards the perimeter of the solid. The next principle is that all the triangular facets must be closed adequately without any gaps between the vertices. Finally, the model should possess a non‐negative coordinate value (Tan and Chen 2016). Analysis of the STL file involves the assessment of the model whether it satisfies all the basic rules.
Two common errors that occur during processing were topological error and normal vector error. Whenever a solid model shares a common vertex, a non‐manifold error would occur that results in topological errors. In such cases, a single solid model was split into two individual models so that the model fixing and repairing would be easier. The latter type of error occurs when the model fails to follow the orientation rule. As a result, the vertices are not closed sufficiently causing normal vector errors. The repair mechanism involves the reordering of the vertex indices in an ordered pattern of triangular facets (Chao et al. 2011). Other common errors encountered during image processing are cracks, holes, voids or missing/ duplicate facets, and flipped orientations (Liu et al. 2009). All these errors fixing and repairing mechanisms are simplified and become easier with modelling software such as Fusion 360, Autodesk ReCap, Trinkle, Sculpteo, MakePrintable, MeshLab, etc. which are specially designed for repairing the STL files ( Table 1.4). These software saves time and helps to improve the printing quality.
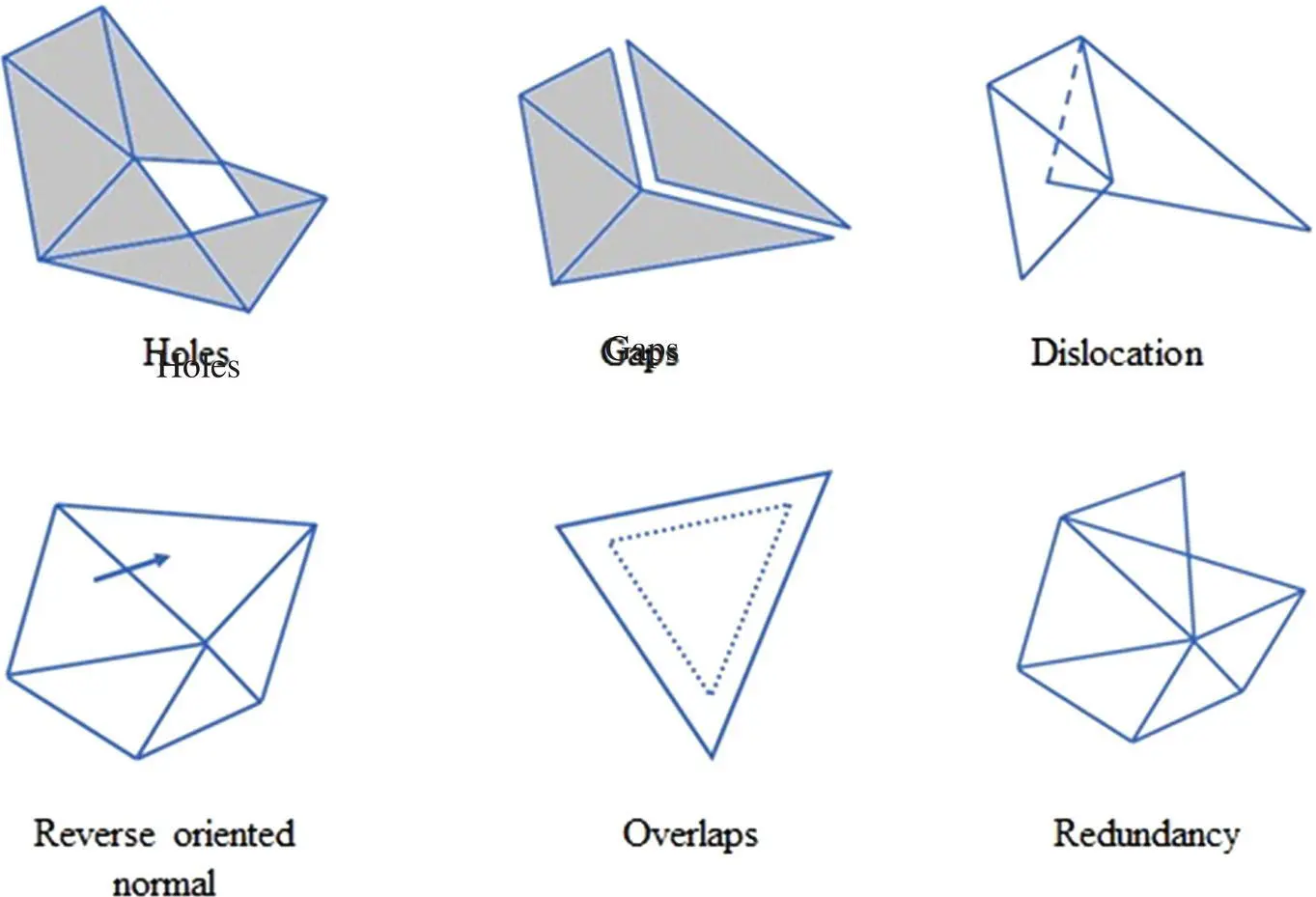
Figure 1.8 Common STL errors.
1.9 Food Printing Platforms
The food printing platform consists of a well‐coordinated XYZ axis system, a dispensing system, and a microprocessor control unit connecting the computer with the printer. The emergence of food printing not only leads to industrial level printing but also makes the possibility of using 3D printers at domestic kitchens. Thus, food 3D printers would become a common kitchen appliance that allows the users to define their own recipes by either downloading the digital recipe files from an online source or creating a new user‐defined digital recipe. Food 3D printing will be a technological cutting edge that helps the users to manipulate the number of ingredients as well as to monitor the calorie intake. Food printing recipes follow two different platforms namely universal, and user‐defined platforms.
1.9.1 Universal Platform
Universal platforms are the existing open‐source printing systems adapted for food applications from allied sectors such as polymer printing. The use of this type of available printing platform for food applications shortens the processing time and saves energy (Sun et al. 2015a). Most of the food printing systems available in the literature were based on universal platforms. Researchers had used these platforms for the printing of food matrices like protein pastes and cake dough and studied the effect of hydrocolloids in textural modification of different food systems (Lipton et al. 2010). A desktop 3D printer, MakerBot was adapted for food printing by modifying the existing extruder head to be suitable for food printing (Millen 2012). Although universal platforms save time and cost, these platforms were not suitable for printing a wide range of food materials since food is a complex matrix comprising of varied physical and chemical composition.
1.9.2 User‐Defined Platform
These are the self‐developed 3D printing platforms created for overcoming the limitations existing with the universal platforms. Based on the specific requirements of printing and the nature of food matrices, self‐developed platforms are defined by users (Hao et al. 2010). These platforms allow the users to have a proportional degree of freedom that helps in achieving flexibility in design components and working mechanisms. Further, these platforms allow for modification and up‐gradation of printing systems. Researchers have developed an in‐house‐built customized extrusion‐based 3D printer CARK (controlled AM robotic kit) specially designed for food applications (Anukiruthika et al. 2020). Here, the components of the printer were selected based on specific requirements for food printing. The developed delta‐based food printer was applicable for printing a wide range of food materials such as food pastes, hydrogels, colloids, etc.
Читать дальшеИнтервал:
Закладка:
Похожие книги на «3D Printing of Foods»
Представляем Вашему вниманию похожие книги на «3D Printing of Foods» списком для выбора. Мы отобрали схожую по названию и смыслу литературу в надежде предоставить читателям больше вариантов отыскать новые, интересные, ещё непрочитанные произведения.
Обсуждение, отзывы о книге «3D Printing of Foods» и просто собственные мнения читателей. Оставьте ваши комментарии, напишите, что Вы думаете о произведении, его смысле или главных героях. Укажите что конкретно понравилось, а что нет, и почему Вы так считаете.