Trinath Sahoo - Root Cause Failure Analysis
Здесь есть возможность читать онлайн «Trinath Sahoo - Root Cause Failure Analysis» — ознакомительный отрывок электронной книги совершенно бесплатно, а после прочтения отрывка купить полную версию. В некоторых случаях можно слушать аудио, скачать через торрент в формате fb2 и присутствует краткое содержание. Жанр: unrecognised, на английском языке. Описание произведения, (предисловие) а так же отзывы посетителей доступны на портале библиотеки ЛибКат.
- Название:Root Cause Failure Analysis
- Автор:
- Жанр:
- Год:неизвестен
- ISBN:нет данных
- Рейтинг книги:5 / 5. Голосов: 1
-
Избранное:Добавить в избранное
- Отзывы:
-
Ваша оценка:
- 100
- 1
- 2
- 3
- 4
- 5
Root Cause Failure Analysis: краткое содержание, описание и аннотация
Предлагаем к чтению аннотацию, описание, краткое содержание или предисловие (зависит от того, что написал сам автор книги «Root Cause Failure Analysis»). Если вы не нашли необходимую информацию о книге — напишите в комментариях, мы постараемся отыскать её.
Provides the knowledge and failure analysis skills necessary for preventing and investigating process equipment failures Root Cause Failure Analysis: A Guide to Improve Plant Reliability
Root Cause Failure Analysis: A Guide to Improve Plant Reliability
Root Cause Failure Analysis — читать онлайн ознакомительный отрывок
Ниже представлен текст книги, разбитый по страницам. Система сохранения места последней прочитанной страницы, позволяет с удобством читать онлайн бесплатно книгу «Root Cause Failure Analysis», без необходимости каждый раз заново искать на чём Вы остановились. Поставьте закладку, и сможете в любой момент перейти на страницу, на которой закончили чтение.
Интервал:
Закладка:
Loading. Where the nature, rate, and magnitude of the applied load correctly anticipated in the design of the part? Were repeated or cyclic loadings involved? What was the direction of the principal stress relative to the shape of the part? Where residual stresses present to an undesirable degree?
Material. Was the recommended alloy used? Where its mechanical properties at the level expected? Where surface or internal discontinuities present that could have contributed to failure? Did the microstructure conform to that prescribed?
Shape. Did the part comply with all pertinent dimensional requirements of the specification? Did the part have sufficient section thickness to prevent local overloading? Where fillets formed with sufficiently large radii? Where there adequate clearances between interacting parts? Where any of the contours deformed during service? Was there evidence of mechanical surface damage?
Environment. Was the part exposed to a corrosive environment or to excessively high or low temperatures? Was the surface of the part suitably protected? Where the properties of the part altered by the exposure? Was there interaction (for example, galvanic) between the material of the part and that of adjacent components?
Fatigue Failures
So far we’ve talked about the gross overloads that can result in immediate, almost instantaneous, catastrophic failures. Another type of failure occurs by means of progressive brittle cracking under repeated alternating or cyclic stresses of an intensity considerably below the normal strength. Although the fracture is of brittle type, it may take some time to propagate, depending on both intensity and frequency of the stress cycles. The number of cycles required to cause fatigue failure at a particular peak stress is quite large but it decreases as stress increases. A very important distinction is that fatigue cracks take time to grow across a part. In a fatigue failure, an incident of a problem can exceed the material’s fatigue strength and initiate a crack that will not result in a catastrophic failure for millions of cycles. There were cases where fatigue failures in 1200 rpm motor shafts that took less than 12 hours from installation to final fracture, about 830 000 cycles. On the other hand, there are cases the crack growth in slowly rotating process equipment shafts has taken many months and more than 10 000 000 cycles to fail.
Fatigue fracture results from the simultaneous action of repeated or fluctuating cyclic stress, tensile stress, and plastic strain. No fatigue crack starts or grows in the absence of any of these three active components. Cyclic stress initiates the crack and tensile stress produces the crack growth. There are many variables in service that influence the fatigue behavior or characteristic pattern. These include the magnitude and frequency of application of the fluctuating stress, the presence of a mean stress, temperature, environment, part size and shape, state of stress and residual stresses, surface finish, surface damages, and microstructure. The occurrence of fatigue may be considered as a three‐stage process.
1 Initiation of the surface or sub‐surface fatigue crack under a fluctuating load.
2 Crack propagation under tensile stress until the section thickness critically bears the imposed load.
3 Sudden fracture under overload
In the presence of a severe stress concentration, multiple crack origins are formed which eventually unite to form a single crack front. When the stress concentration on the surface is absent, cracks propagate more readily near the center of a section than at the surface. While there is a stress concentrating ‘notch, W‐shaped crack fronts are‐observed. For a given material, zone of the final fracture increases with increasing applied load. On rotating or bending the final fracture’, region is often rotated or offset toward the origin in the direction opposite to the direction of rotation. Also, with increasing nominal stress, the final fracture moves toward the center.
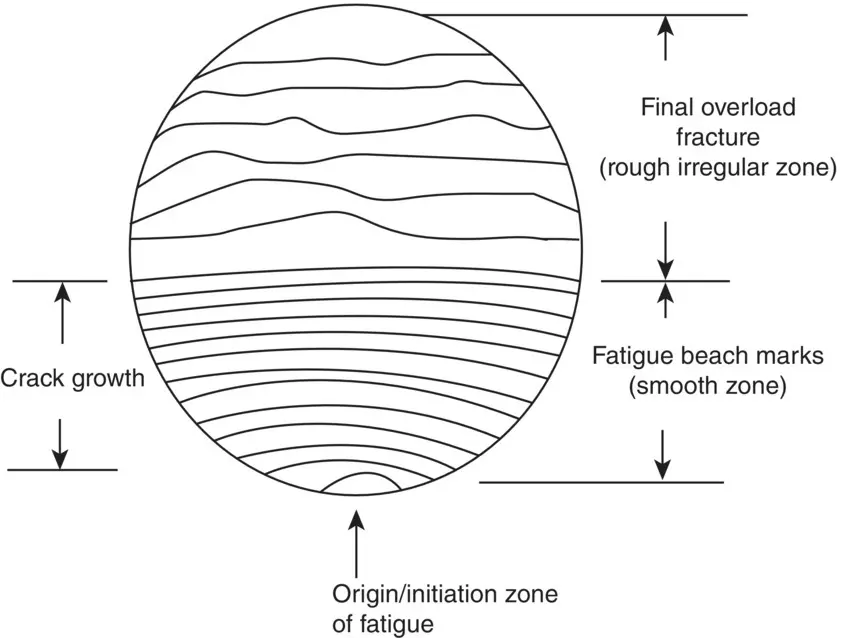
Figure 5.9Schematic representation of the fatigue crack (three stage) phenomenon.
Stress Concentration
A stress concentration is a physical or metallurgical condition that increases the local stress in the part by some factor. A good example is the shaft shown in Figure 5.10. We see that the stress in the area of the radius varies depending on the size of the radius. A small radius can increase the stress dramatically
Thermal Fatigue Failure
Thermal fatigue failure is the result of repeated thermal cycling which generates repeated stress gradients within a free component or stress cycling within a component constrained to fixed dimensions. Thermal fatigue fractures are characterized by surface cracking formed by multiple initiation sites that join randomly by edge sliding to form the main crack. Other features to identify thermal fatigue are as follows:
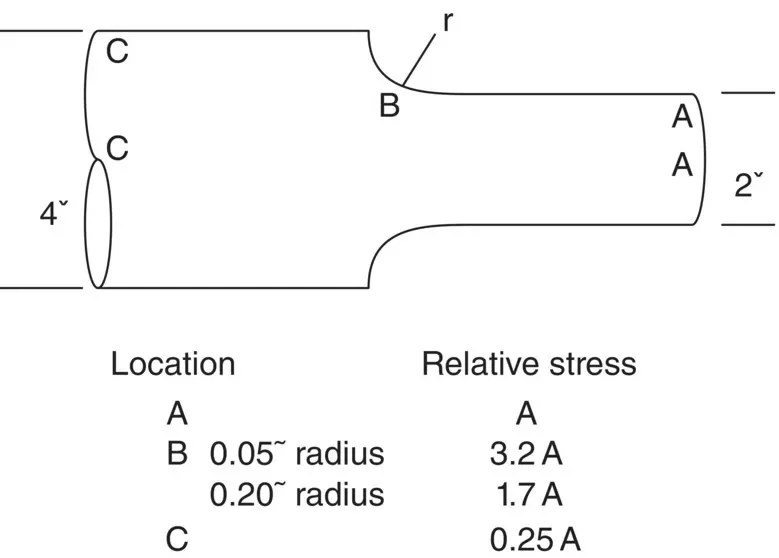
Figure 5.10 Stress concentration at corners.
Fractures are planner and transverse with no visible plastic deformation.
Fracture is mostly transgranular.
Oxidized fracture surfaces and oxide wedge filled cracks further characterize thermal fatigue failures
Fatigue resistance is affected by a number of controllable factors:
The chemistry of the material and its resultant microstructure have a profound effect on fatigue strength. In fact, they can equally influence on mechanical strength (tensile and yield). Alloying elements, such as chromium, nickel, and moly, have the greatest effect on the iron base system. Solid solution alloys show the maximum increase in fatigue strength.
Grain size appears to be a strong determining factor in inhibiting the plastic deformation process that occurs with crack propagation.
Environmental factors such as cyclic temperature, temperature gradient, and corrosion pitting that result in stress concentrations. The thermal fatigue failure shown in was due to the temperature gradient across the thick wall section.
Reduction of localized surface stress concentrations by such techniques as case hardening, shot peening, auto frottage, and thread rolling.
Proper heat treatment can markedly improve fatigue resistance. As an example, for steels, a tempered martensitic.
Stress Corrosion Cracking
Stress corrosion cracking (SCC) is a fracture process that involves the combined and simultaneous action of a tensile stress and a corrosive environment. SCC occurs when the tensile stress and a specific environment are able to cause failure by their combined action, but are insufficient to cause failure by either one acting alone. In fact, the tensile stresses are usually below the metal’s yield strength. Furthermore, the metal would suffer only minimal corrosion in the absence of the applied stress. The problem itself can be quite complex. The situation with buried pipelines is a good example of such complexity.
There are three requirements for SCC to occur:
1 A susceptible metal.
2 Tensile stresses applied to the metal.
3 A specific environment containing an aggressive species that promotes SCC.
This form of corrosion is particularly dangerous because it may not occur under a particular set of conditions until there is an applied stress. The corrosion is not clearly visible prior to fracture and can result in catastrophic failure. Many alloys can experience stress corrosion, and the applied stress may also be due to a residual stress in the material. An example of a residual stress could be a stress remaining in a material after forming, or a stress due to welding. Stress corrosion cracking will usually cause the material to fail in a brittle manner, which can have grave consequences as there is usually little or no warning before the failure occurs.
Читать дальшеИнтервал:
Закладка:
Похожие книги на «Root Cause Failure Analysis»
Представляем Вашему вниманию похожие книги на «Root Cause Failure Analysis» списком для выбора. Мы отобрали схожую по названию и смыслу литературу в надежде предоставить читателям больше вариантов отыскать новые, интересные, ещё непрочитанные произведения.
Обсуждение, отзывы о книге «Root Cause Failure Analysis» и просто собственные мнения читателей. Оставьте ваши комментарии, напишите, что Вы думаете о произведении, его смысле или главных героях. Укажите что конкретно понравилось, а что нет, и почему Вы так считаете.