Trinath Sahoo - Root Cause Failure Analysis
Здесь есть возможность читать онлайн «Trinath Sahoo - Root Cause Failure Analysis» — ознакомительный отрывок электронной книги совершенно бесплатно, а после прочтения отрывка купить полную версию. В некоторых случаях можно слушать аудио, скачать через торрент в формате fb2 и присутствует краткое содержание. Жанр: unrecognised, на английском языке. Описание произведения, (предисловие) а так же отзывы посетителей доступны на портале библиотеки ЛибКат.
- Название:Root Cause Failure Analysis
- Автор:
- Жанр:
- Год:неизвестен
- ISBN:нет данных
- Рейтинг книги:5 / 5. Голосов: 1
-
Избранное:Добавить в избранное
- Отзывы:
-
Ваша оценка:
- 100
- 1
- 2
- 3
- 4
- 5
Root Cause Failure Analysis: краткое содержание, описание и аннотация
Предлагаем к чтению аннотацию, описание, краткое содержание или предисловие (зависит от того, что написал сам автор книги «Root Cause Failure Analysis»). Если вы не нашли необходимую информацию о книге — напишите в комментариях, мы постараемся отыскать её.
Provides the knowledge and failure analysis skills necessary for preventing and investigating process equipment failures Root Cause Failure Analysis: A Guide to Improve Plant Reliability
Root Cause Failure Analysis: A Guide to Improve Plant Reliability
Root Cause Failure Analysis — читать онлайн ознакомительный отрывок
Ниже представлен текст книги, разбитый по страницам. Система сохранения места последней прочитанной страницы, позволяет с удобством читать онлайн бесплатно книгу «Root Cause Failure Analysis», без необходимости каждый раз заново искать на чём Вы остановились. Поставьте закладку, и сможете в любой момент перейти на страницу, на которой закончили чтение.
Интервал:
Закладка:
Different Levels of Causes
A failure is often the result of multiple causes at different levels. Some causes might affect other causes that, in turn, create the visible problem. Causes can be classified as one of the following:
Symptoms. These are not regarded as actual causes, but rather as signs of existing problems.
First‐level causes. Causes that directly lead to a problem.
Higher‐level causes. Causes that lead to the first‐level causes. They may not directly cause the problem, but form links in the chain of cause‐and‐effect relationships that ultimately create the problem.
Some failures often have compound reasons, where different factors combine to cause the problem. Examples of the levels of causes follow.
The highest‐level cause of a problem is called the root cause:
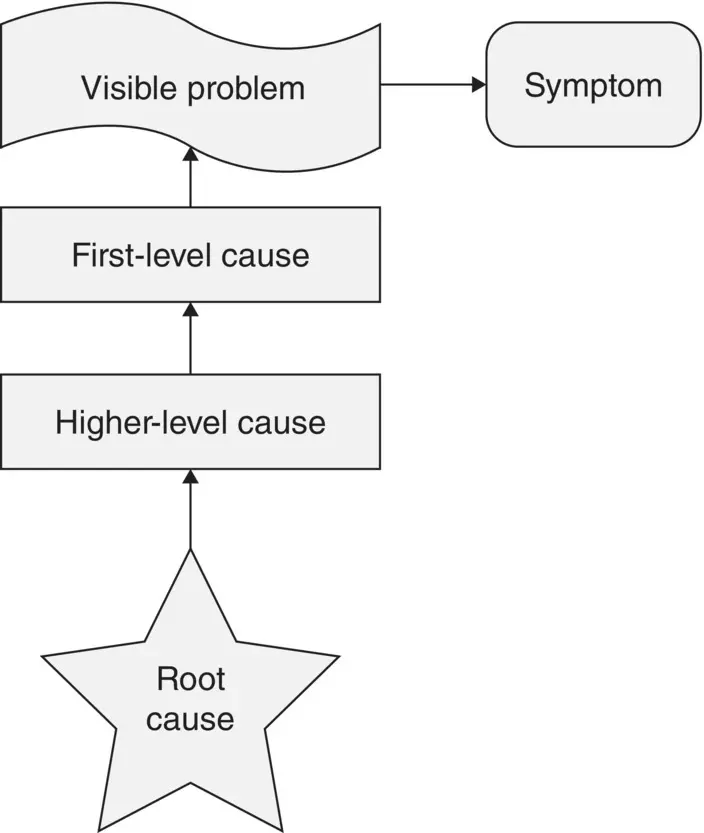
Hence, the root cause is “the evil at the bottom” that sets in motion the entire cause‐and‐effect chain causing the problem(s).
TrevoKletz said
…root cause investigation is like peeling an onion. The outer layers deal with technical causes, while the inner layers are concerned with weaknesses in the management system. I am not suggesting that technical causes are less important. But putting technical causes right will prevent only the LAST event from happening again; attending to the underlying causes may prevent MANY SIMILAR INCIDENCES.
The difference between failure analysis and root cause analysis is that failure analysis is a discipline used for identifying the physical roots of failures, whereas the root cause analysis (RCA) techniques is a discipline used in exploring some of the other contributors to failures, such as the human and latent root causes. Root cause analysis is intended to identify the fundamental cause(s) that if corrected will prevent recurrence. The principles of RCA may be applied to ensure that the real root cause is identified to initiate appropriate corrective actions. RCA helps in correcting and preventing failures, achieving higher levels of quality and reliability, and ultimately enhancing customer satisfaction
Depending on the objectives of the RCA, one should decide how deeply one should analyze the case. These objectives are typically based on the risk associated with the failures and the complexity of the situation. The three levels of root cause analysis are physical roots, human roots, and latent roots. Physical roots, or the roots of equipment problems, are where many failure analyses stop. Physical root causes are derived from laboratory investigation or engineering analysis and are often component‐level or materials‐level findings. Human roots (i.e., people issues) involve human factors, where the error may be happened due to human judgment that may have caused the failure. Latent roots include roots that are organizational or procedural in nature, as well as environmental or other roots that are outside the realm of control.
Physical Roots
This is the physical mechanism that caused the failure, it may be fatigue, overload, wear, corrosion, or any combination of these. For example – corrosion damage of a pipeline, a bearing failed due to fatigue. Failure analysis must start with accurately determining the physical roots, for without that knowledge, the actual human and latent roots cannot be detected and corrected. The analysis may focus on physics of the incident. In the case of TITANIC, the iron rivets were too weak .
The steel plates of the TITANIC buckled as there were excessive stress applied to the hull when the ship hit the iceberg. The strength of steel and hull was not sufficient to prevent the hull from being breached by the steel plates buckling. The failure of the hull steel resulted from brittle fractures caused by the high sulfur content of the steel, the low temperature water on the night of the disaster, and the high impact loading of the collision with the iceberg. When the TITANIC hit the iceberg, the hull plates split open and continued cracking as the water flooded the ship.
Human Roots
The human roots are those human errors that result in the mechanisms that caused the physical failures. What is the error committed that lead to the physical cause?
Someone did the wrong thing knowingly or unknowingly. We asked what caused the person to commit this mistake. A good example is, the TITANIC was sailing full speed ahead despite concerns about icebergs was Smith’s biggest misstep. the TITANIC was actually speeding up when it struck the iceberg as it was White Star chairman and managing director, Bruce Ismay’s, intention to run the rest of the route to New York at full speed, arrive early, and prove the TITANIC’s superior performance. Ismay survived the disaster and testified at the inquiries that this speed increase was approved by Captain Smith and the helmsman was operating under his Captain’s direction.
Latent Roots
All physical failures are triggered by humans. But humans are negatively influenced by latent forces. The goal is to identify and remove these latent forces. Latent causes reveal themselves in layers. One after the other, the layers can be peeled back, similar to peeling the layers off an onion. It often seems as if there is no end. These forces within the organizations are causing people to make serious mistakes.
These are the management system weaknesses that include training, policies, procedures and specifications. People make decision based on these and if the system is flawed, the decision will be in error and will be the triggering mechanism that causes the mechanical failure to occur. These are the management system weaknesses. These include training, policies, procedures and specifications. The most proactive of all industrial action might be to identify and remove these latent traps. But all our attempts to identify and remove these latent causes of failure start at the human. Humans do things “inappropriately,” for “latent” reasons. In order to understand these reasons, we must first understand what “errors” are being made. This puts people at risk – especially the “culprits.” Once exposed. They are in danger of being inappropriately disciplined.
In the TITANIC case, the voyage had been so hastily pushed that the crew had no specific training or conducted any drills in lifesaving on the TITANIC, being unfamiliar with the lifeboats and their davit lowering mechanisms. Compounding this was a decision by White Star management to equip the TITANIC with only half the necessary lifeboats to handle the number of people onboard. The reasons are long established. White Star felt a full complement of lifeboats would give the ship an unattractive, cluttered look. They also clearly had a false confidence the lifeboats would never be needed.
To understand different level of root causes, let us take one industrial case.
Consider this example: During the overhauling of a large reciprocating compressor, the maintenance supervisor discovers a damaged compressor rod requiring replacement. So, he decides to have a rod made in a local shop by fabricating the rod with cut threads. But the OEM’s design department has recommended the compressor rods for this frame size to have rolled threads. As a result of the improper fabrication, the rod fails due to fatigue in the thread area and causes extensive secondary damage inside the compressor.
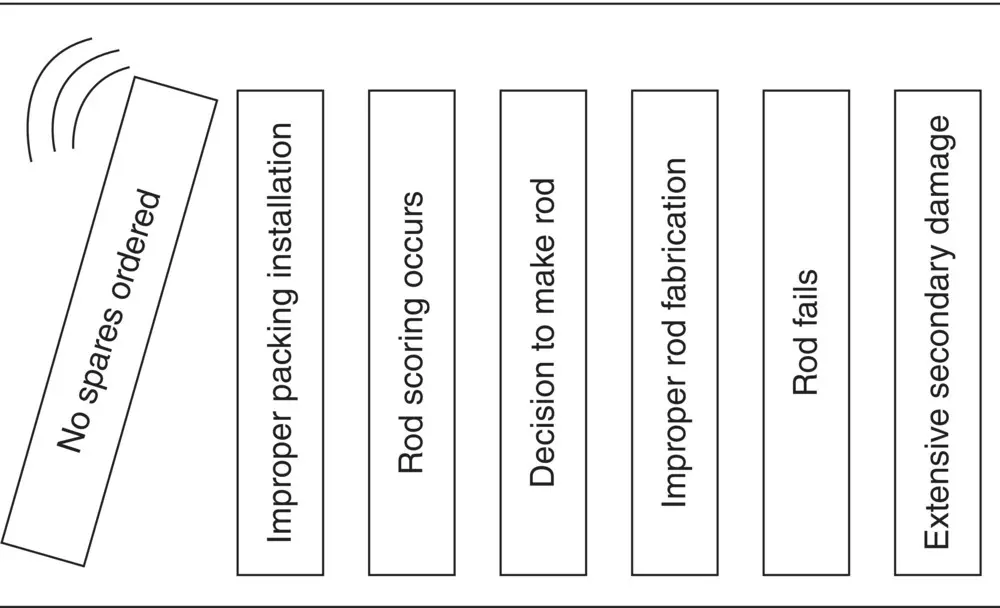
Figure 2.1Events leading to compressor failure.
Читать дальшеИнтервал:
Закладка:
Похожие книги на «Root Cause Failure Analysis»
Представляем Вашему вниманию похожие книги на «Root Cause Failure Analysis» списком для выбора. Мы отобрали схожую по названию и смыслу литературу в надежде предоставить читателям больше вариантов отыскать новые, интересные, ещё непрочитанные произведения.
Обсуждение, отзывы о книге «Root Cause Failure Analysis» и просто собственные мнения читателей. Оставьте ваши комментарии, напишите, что Вы думаете о произведении, его смысле или главных героях. Укажите что конкретно понравилось, а что нет, и почему Вы так считаете.